An automotive supplier in Mexico is to produce new tail lights with OLED modules for a customer. Due to successful projects in the past with the company, Robooptic Systems was consulted for the development of the production line and entrusted with the task of planning and manufacturing a system for the fully-automated assembly and 100 % end-of-line testing of OLED tail lights.
100% End-of-Line-Test 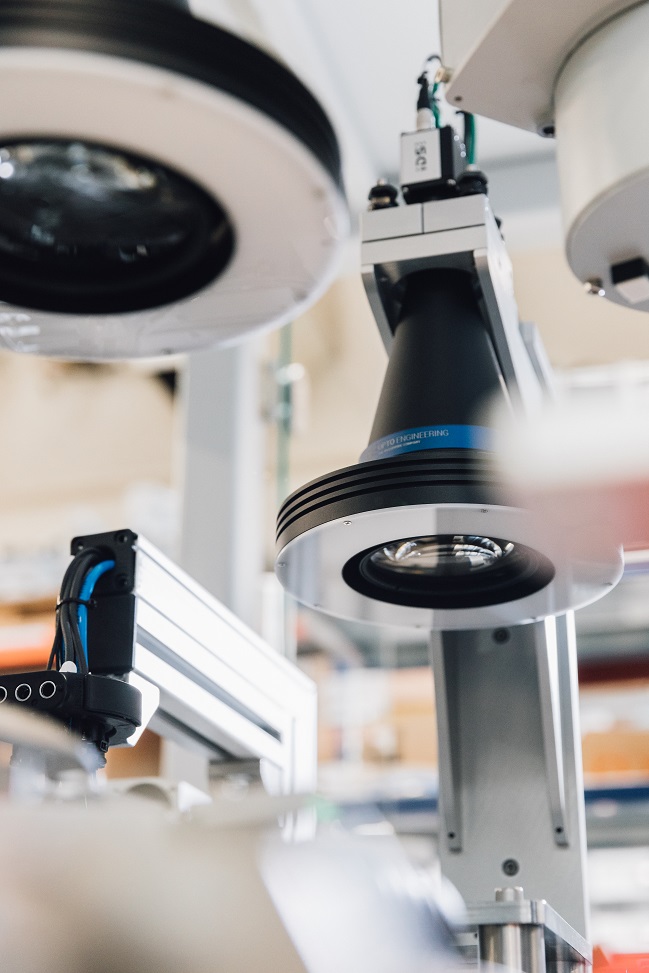
To meet market requirements, the system must perform a 100 % end-of-line test. This means that in addition to gluing the OLED segments to a plastic carrier with an accuracy of 0.01 mm, 100 % of the illuminated area of the elements must also be tested. If a segment has a too weak luminosity or a so-called dark spot (non-luminous point in the OLED light area) that is larger than 100 μm, the OLED segment must be rejected and replaced.
Poka- Yoke procedure
Important for the customer was the simple operation of the line using the POKA-YOKE procedure, as well as a fast cycle time in order to be able to produce as many products as possible in one shift. Of course, ergonomics for the workers working on the system was also a concern of the customer.
Special product carriers ensure 100 % fault exclusion
Although the assembly of the tail lights is fully automatic in the machine, the individual parts must be fed by workers at two input points of the system. Special product carriers have been developed for this purpose, which, due to their special shape, can only be inserted into the system at the correct input position. As a result, it is not possible to insert the parts in the wrong place or in a wrong position in the process. After manual feeding of the individual parts, the two robots inside the system start assembling the product. For precise bonding of the OLED elements on the plastic carrier, several cameras are used in conjunction with the robot arms for precise positioning to within 0.01 mm.
End-of-Line-Station
At the end-of-line station within the machine, the finished bonded OLED elements are then inspected for luminous paint, luminosity, cracks and scratches, pixel errors and power consumption. If the test is OK, the finished product can be removed at the front of the machine.
Employee protection
To meet the ergonomic requirements of the customer, the working height and the height of the control panels were adapted to the customer's wishes in accordance with the specifications of the production manager on site. A simple menu navigation in the software and transport support in the form of a trolley for feeding the product carriers to the machine were also included for this purpose.
Core competences in the project
Summary of customer benefit
Fast cycle time in a dust-free and self-contained processing system for OLED elements with full inspection and automatic exclusion of N-OK parts. Easy operation due to two feed points with predefined product carriers.
A German company specialising in the production of light microscopes contacted us for a new product line because of our experience with machine vision. These are microscopes for surgical applications, which, with the help of a micro-projector application, are intended to display a new light spectrum invisible to the human eye.
Digital image overlay using AR technology
The new microscope is to be equipped with an image injection module to provide an AR (Augmented Reality) overlay, which normally displays non-visible light spectra on an output screen. The image must be taken in real time and displayed overlapping with the magnified images of the microscope.
Since medical technology is naturally subject to the strictest quality standards, every product delivered must be assembled under clean-room conditions and tested for 100 % error-free operation.
UV or IR light, not visible with the human eye, is made visible
Several test set-ups for the optical design of micro multichannel CCD cameras were evaluated under clean-room conditions and a solution for series production was found in collaboration with the customer. Thanks to the use of a 3-CCD camera, the spectrum of the light is divided into different wavelength bands, each of which falls on a special CCD chip. This improves the spectral performance of the microscope, making it possible to see UV or IR light that cannot be seen with the human eye. This amplification in the recording of the light spectrum is used for the medical applications of the microscope.
Thanks to the use of 3-CCD technology, light spectra can be recorded with the surgical microscope and projected onto an external screen, which would not be visible with the human eye.
Core competences in the project
Summary of customer benefit
Thanks to the use of 3-CCD technology, light spectra can be recorded with the surgical microscope and projected onto an external screen, which would not be visible with the human eye.
To increase productivity in testing and packaging of grinding wheels, an Austrian abrasives manufacturer wants to automate the work steps that were previously carried out manually on conveyor belts at the end of the production chain. By applying our expertise with vision systems, we are to design an end-of-line testing station including a Teflon remover, which takes over the simple tasks previously performed by the operators.
Cylce time of ≤ 2 sec.
With a cycle time of less than 2 seconds per wheel, the End-of-Line station will perform a fully-automated test of the grinding wheels as previously performed manually by the operators. This means that circumference, outer contour as well as inner contour, flatness and thickness are measured by means of several camera systems, evaluated and automatically sorted out if there is too much deviation from standard values.
Ensuring traceablility
It was particularly important for the customer that the system automatically rejects discs that do not meet the requirements of the abrasives industry. The machine should provide a more accurate and above all faster inspection of the products than was previously possible manually. The operators, who were previously responsible for the inspection, should be able to fill the machine without much effort and randomly take individual discs for checking.
The system must meet the requirements of the applicable regulations for the abrasive industry
The system processes grinding and cut-off wheels. The cut-off wheels are separated using Teflon wheels for the furnace process. During automatic processing of the wheels, the cut-off wheels must be separated from the Teflon wheels. This is done by means of a specially developed process. The process draws the Teflon from the discs without damaging the discs.
Disc testing is carried out by an automatic disc tester in the machine and meets the requirements of the applicable regulations for the abrasives industry. Each disc is checked for production faults or cracks on the outer and inner contours, circumference, flatness and thickness. For purposes of traceability, each product is assigned a serial number.
The cycle time depends on the size of the disc and is approximately 2 sec.
Core competences in the project
Summary of customer benefit
Faster and fully-automatic process flow from the furnace to packaging in one system. Operators who previously required high concentration when checking grinding wheels manually can now deliver faster results by simply filling the machine, while wheels that do not meet the requirements are sorted out fully automatically.
A manufacturer of electronic measuring devices in Singapore wants to speed up the production of laser distance meters. Using our advanced vision systems, we can offer a rotary table solution with a fully-automated, high-precision gluing process and high cycle time.
High-precision measuring tools with special quality standards
Laser distance meters are high-precision measuring tools that are used in many different industries. Obviously, to ensure this precision of the finished product, a number of special quality standards must be observed during production. For example, precise alignment of only a few μm of the lens must be ensured in order to focus the light of the laser.
Fast cycle time with high quality
It was particularly important for the customer to ensure the fastest possible cycle time with a high quality standard. A particular challenge was to design the system to accommodate several different module housings of the laser distance meters, so that different products can be processed without retooling.
Two device types in one product recaptacle
On a rotary indexing table, the receiving lens and the diamond window are mounted and fixed in the module housing of a laser distance meter at ten stations. Two types of devices are to be processed, whereby the various module housings are mounted on a common carrier system. Receiving lens and diamond window are glued to the module housing with a UV-curing adhesive. The bonding also functions as a seal.
Core competences in the project
Summary of customer benefit
The customer can equip several different module housings with one machine without time-consuming retooling, while guaranteeing a high quality standard with a fast cycle time.