Ein Automobilzulieferunternehmen in Mexiko soll für einen Kunden neue Rücklichter mit OLED-Modulen produzieren. Durch erfolgreiche Projekte in der Vergangenheit mit dem Unternehmen wurde Robooptic Systems zur Entwicklung der Produktionslinie hinzugezogen und mit der Aufgabe betraut, eine Anlage für den vollautomatischen Zusammenbau und den 100%-igen End-of-Line-Test von OLED-Rücklichtern zu planen und herzustellen.
100% End-of-Line-Test 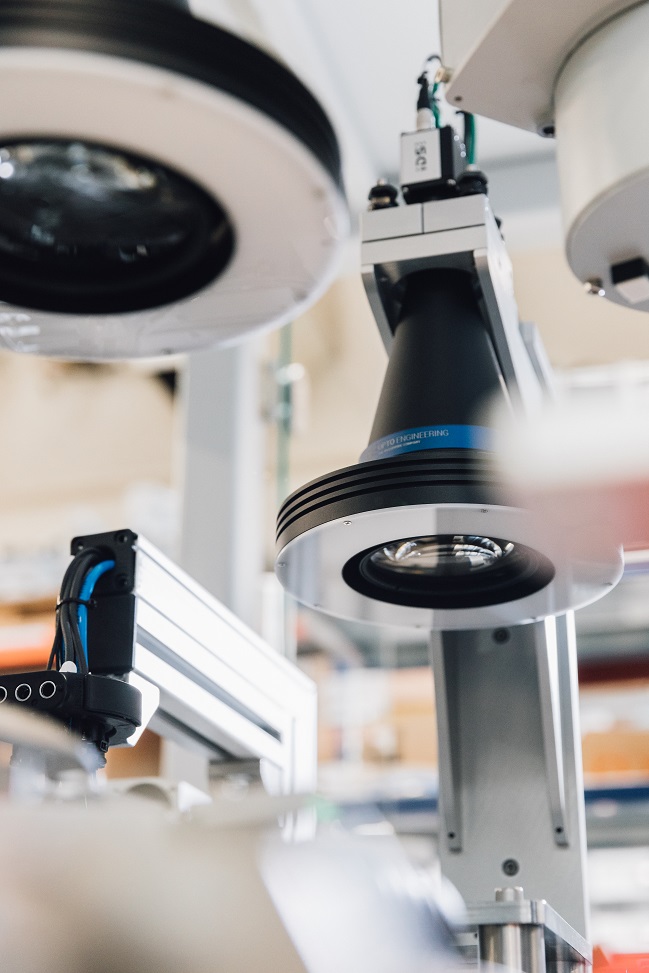
Um den Markterfordernissen gerecht zu werden, muss die Anlage einen 100% End-of-Line-Test durchführen. Das bedeutet, dass neben einem auf 0.01 mm genauen Verkleben der OLED-Segmente auf einen Plastikträger auch 100% der Leuchtfläche der Elemente geprüft werden muss. Sollte ein Segment eine zu schwache Leuchtkraft oder einen sogenannten Dark-Spot (nicht leuchtenden Punkt im OLED-Leuchtbereich) der größer als 100 μm ist aufweisen, muss das OLED-Segment ausgeschieden und ersetzt werden.
Poka- Yoke Verfahen
Wichtig für den Kunden war die einfache Bedienung der Anlage mithilfe des POKA-YOKE Verfahrens sowie eine schnelle Taktzeit, um möglichst viele Produkte in einer Schicht produzieren zu können. Natürlich war auch die Ergonomie für die an der Anlage arbeitenden Arbeiter ein Anliegen des Kunden.
Spezielle Produktträger sorgen für 100% Fehlerausschluss
Der Zusammenbau der Rücklichter erfolgt zwar vollautomatisch in der Maschine, doch die Zufuhr der Einzelteile muss durch Arbeiter an zwei Eingabepunkten der Anlage geschehen. Hierfür wurden spezielle Produktträger entwickelt, die durch ihre besondere Formgebung nur an die richtige Eingabeposition in die Anlage eingebracht werden können. Dadurch ist es nicht möglich die Einzelteile an einer falschen Stelle oder in einer falschen Lage dem Prozess Nach manueller Zuführung der Einzelteile starten die zwei Roboter im inneren der Anlage mit dem Zusammenbau des Produkts.Für eine präzise Verklebung der OLED-Elemente auf den Kunststoff-Träger werden mehrere Kameras genutzt, die in Zusammenspiel mit den Roboterarmen für die 0.01 mm genauen Positionierung.
End-of-Line-Station
An der End-of-Line-Station innerhalb der Maschine werden dann die fertig verklebten OLED-Elemente auf Leuchtfarbe, Leuchtkraft, Risse und Kratzer, Pixelfehler sowie Stromverbrauch geprüft. Ist die Prüfung in Ordnung, kann das fertige Produkt an der Vorderseite der Maschine entnommen werden.
Arbeitnehmerschutz
Um die ergonomischen Anforderungen des Kunden zu erfüllen, wurden in Abstimmung mit den Angaben des Produktionsleiters vor Ort die Arbeitshöhe und die Höhe der Bedienpanels auf Kundenwunsch angepasst. Eine einfache Menüführung in der Software und eine Transportunterstützung in Form eines Trollys zur Zuführung der Produktträger zur Maschine wurden ebenfalls zu diesem Zweck mit eingeplant.
Kernkompetenzen im Projekt
Zusammenfassung des Kundennutzen
Schnelle Taktzeit in einem staubfreien und in sich geschlossenen Bearbeitungssystems für die OLED-Elemente mit vollständiger Überprüfung und automatischem Ausschluss von N-OK Teilen. Einfache Bedienung durch zwei Zuführpunkte mit vordefinierten Produktträgern.
Ein deutsches Unternehmen, dass sich auf die Herstellung von Lichtmikroskopen spezialisiert hat, wendete sich dank unseren Erfahrungen im maschinellen Sehen an uns, um eine neue Produktreihe auf den Markt zu bringen. Hierbei handelt es sich um Mikroskope für chirurgische Anwendungen, welche mithilfe von einer Mikro-Projektor-Anwendung ein neues, für das menschliche Auge unsichtbares Lichtspektrum darstellen soll.
Digitale Bildüberlagerung durch AR-Technik
Das neue Mikroskop soll mithilfe eines Bildinjektionsmoduls eine AR-Einblendung (Augmented Reality-Einblendung) bekommen, die normalerweise nicht sichtbare Lichtspektren auf einen Ausgabebildschirm darstellt. Die Aufnahme muss dabei in Echtzeit erfolgen und überlappend mit den vergrößerten Bildern des Mikroskops ausgegeben werden.
Da die Medizintechnik natürlich strengsten Qualitätsstandards unterlieg, muss jedes ausgelieferte Produkt unter Reinraumbedingungen zusammengebaut und auf 100% fehlerfreie Funktion geprüft werden.
UV- oder IR-Licht, mit dem menschlichen Auge nicht erkennbar, wird sichtbar gemacht
Unter Reinraumbedingungen wurden mehrere Versuchsaufbauten für das optisches Design von Mikro-Mehrkanal-CCD-Kameras ausgewertet und in Zusammenarbeit mit dem Kunden eine Lösung für die Serienproduktion gefunden. Dank der Verwendung einer 3-CCD-Kamera wird das Spektrum des Lichts in verschiedene Wellenlängenbänder aufgeteilt, die jeweils auf einen spezielle CCD-Chip fallen. Dies verbessert die spektrale Leistung des Mikroskops, wodurch es möglich ist, UV- oder IR-Licht zu sehen, das mit dem menschlichen Auge nicht gesehen werden kann. Diese Verstärkung in der Aufnahme des Lichtspektrums wird für die medizinischen Anwendungen des Mikroskops genutzt.
Kernkompetenzen im Projekt
Zusammenfassung des Kundennutzen
Dank der Nutzung der 3-CCD-Technologie können Lichtspektren mit dem chirurgischen Mikroskop aufgenommen und auf einen externen Bildschirm projiziert werden, welche mit dem menschlichen Auge nicht erkennbar wären.
Um die Produktivität beim Testen und Verpacken von Schleifscheiben zu steigern, möchte ein österreichischer Schleifmittelhersteller die bisher Manuel auf Fließbändern ausgeführten Arbeitsschritte am Ende der Produktionskette automatisieren. Durch gezielten Einsatz unserer Expertise mit Vision Systemen, sollen wir eine End-of-Line Prüfstation inklusive eines Teflonablösers entwerfen, die die einfachen arbeiten, die zuvor von Arbeitern ausgeführt wurden, übernehmen.
Taktzeit von ≤ 2 sec.
Mit einer Taktzeit von unter 2 Sekunden pro Scheibe soll die End-of-Line Station eine vollautomatische Prüfung der Schleifscheiben durchführen, wie sie zuvor manuell von den Arbeitern durchgeführt wurde. Das heißt, es werden Umfang, Außenkontur- sowie Innenkontur, Ebenheit und Dicke mithilfe von mehreren Kamerasystemen vermessen, ausgewertet und bei zu großer Abweichung von Standardwerten automatisch aussortiert.
Gewährleistung der Rückverfolgbarkeit
Für den Kunden war es besonders wichtig, dass die Anlage Scheiben, die nicht den Anforderungen der Schleifmittelindustrie entsprechen, automatisch aussortiert werden können. Die Maschine soll eine genauere und vor allem schnellere Überprüfung der Produkte liefern als es bisher manuell der Fall war. Die Arbeiter, die zuvor für die Überprüfung zuständig waren, sollen die Maschine ohne großen Aufwand befüllen und Stichprobenmäßig einzelne Scheiben zum Check entnehmen können.
Anlage muss Anforderungen der geltenden Regelwerke für die Schleifmittelindustrie entsprechen.
Die Anlage verarbeitet Schleif- und Trennscheiben. Die Trennscheiben werden mittels Teflon Scheiben für den Ofenprozess getrennt. Bei der automatischen Verarbeitung der Scheiben müssen die Trennscheiben von den Teflon Scheiben getrennt werden. Das erfolgt mit einem eigens entwickelten Verfahren. Das Verfahren zieht das Teflon von den Scheiben, ohne die Scheiben zu beschädigen.
Die Scheibenprüfung erfolgt über einen automatischen Scheiben Tester in der Maschine und entspricht den Anforderungen der geltenden Regelwerke für die Schleifmittelindustrie. Jede Scheibe wird auf etwaige Produktionsfehler oder Sprünge an der Außen- sowie Innenkontur, den Umfang, die Ebenheit und die Dicke überprüft. Zur Rückverfolgbarkeit wird jedes Produkt mit einer Seriennummer versehen.
Die Taktzeit ist abhängig von Scheibengröße und liegt bei ca. 2 sec.
Kernkompetenzen im Projekt
Zusammenfassung des Kundennutzen
Schnellerer und voll automatischer Prozessablauf vom Ofen bis zur Verpackung in einer Anlage. Die Arbeiter die zuvor hohe Konzentration bei der manuellen Übprüfung der Schleifscheiben benötigten, können nun schnellere Ergebnisse durch einfaches Befüllen der Maschine liefern, wärend Scheiben die nicht den Anforderungen entsprechen vollautomatisch Aussortiert werden.
Ein Hersteller elektronischer Messgeräte in Singapur möchte die Produktion von Laserentfernungsmessgeräten beschleunigen. Mithilfe unserer ausgeprägten Bildverarbeitungssystemen können wir eine Rundtakttisch-Lösung mit einem vollautomatischen, hochpräzisen Klebeprozess und hoher Taktzeit anbieten.
Hochpräzise Messwerkzeuge mit besonderen Qualitätsstandards
Laserentfernungsmessgeräte sind hochpräzise Messwerkzeuge, welche in vielen verschiedenen Branchen Anwendung finden. Um diese Präzision des fertigen Produkts zu gewährleisten, müssen bei der Produktion natürlich einige besondere Qualitätsstandards eingehalten werden. Eine nur wenige im μm genaue Ausrichtung der Linse muss beispielsweise sichergestellt werden, um das Licht des Lasers zu fokussieren.
Schnelle Taktzeit bei hoher Qualität
Für den Kunden war es besonders wichtig eine möglichst schnelle Taktzeit bei hohem Qualitätsstandard zu gewährleisten. Eine besondere Herausforderung war es, die Anlage auf mehrere unterschiedliche Modulgehäuse der Laserentfernungsmessgeräte auszulegen, sodass unterschiedliche Produkte ohne Umrüsten bearbeitet werden können.
Zwei Gerätetypen in einer Produktaufnahme
Auf einem Rundtakttisch erfolgt im getakteten Rundlauf an zehn Stationen die Montage und Fixierung der Empfangslinse und des Rautenfensters in das Modulgehäuse eines Laserentfernungsmessgerätes. Vorgesehen ist die Verarbeitung von zwei Gerätetypen, wobei die Aufnahme der verschiedenen Modulgehäuse auf einem gemeinsamen Trägersystem erfolgt. Empfangslinse und Rautenfenster werden durch einen UV-härtenden Kleber mit dem Modulgehäuse verklebt. Die Verklebung funktioniert gleichzeitig als Abdichtung.
Kernkompetenzen im Projekt
Zusammenfassung des Kundennutzen
Der Kunde kann mit einer Maschine mehrere unterschiedliche Modulgehäuse ohne zeitaufwendiges Umrüsten bestücken und dabei einen hohen Quaitätsstandard bei schneller Taktzeit gewährleisten.